I recently completed this mirror and wall cabinet, named Echo and Narcissus. They are made of black walnut and Douglas-Fir and both feature curved elements.
The front face and doors of the wall cabinet, Echo, are curved. I made the curved doors by gluing up a 5-layer core of shop-sawn veneers over a curved form, alternating the grain direction of each ply. Then I pressed decorative Douglas-Fir veneers onto the outside and inside faces of each door.
The mirror, Narcissus, has a curved "crown" with decorative Douglas-Fir veneer. The process for this crown was slightly different. Using the same curved form, I glued up a 5-layer core of shop sawn veneers. Because the crown would be contained somewhat by the black walnut above and below, I didn't alternate the grain direction of the plies. Once the core was laid up, I pressed the decorative Douglas-Fir face veneer to the outside face.
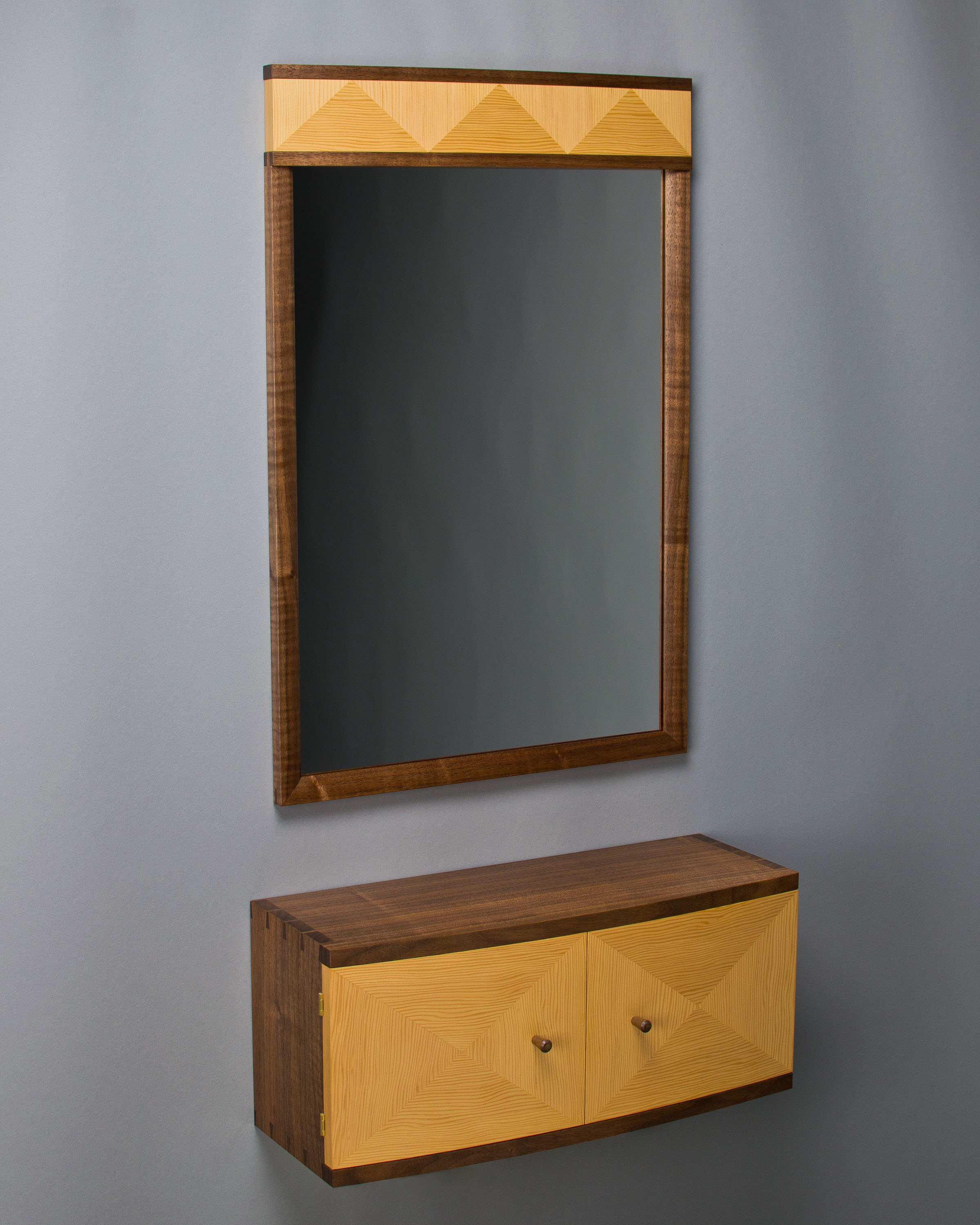
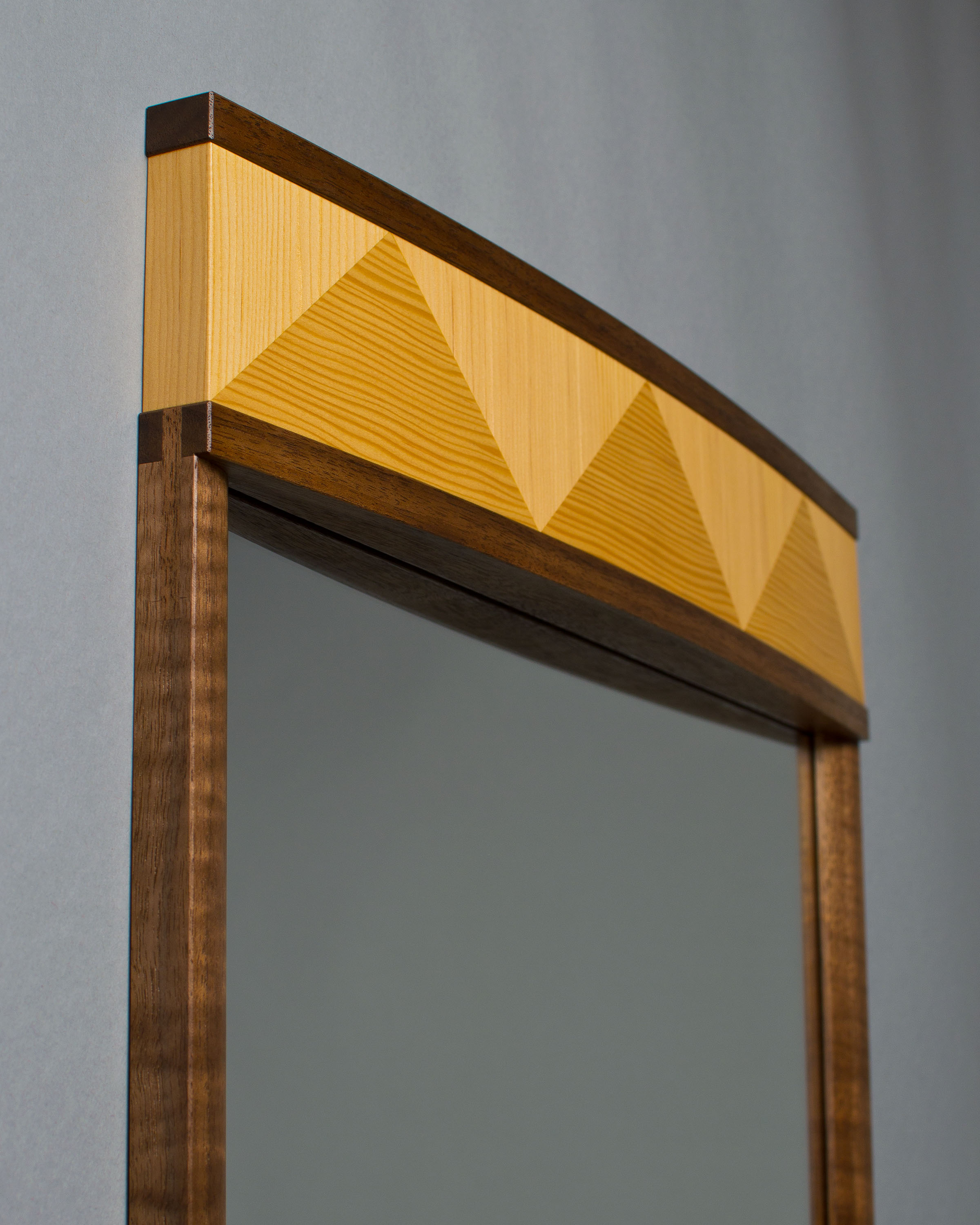
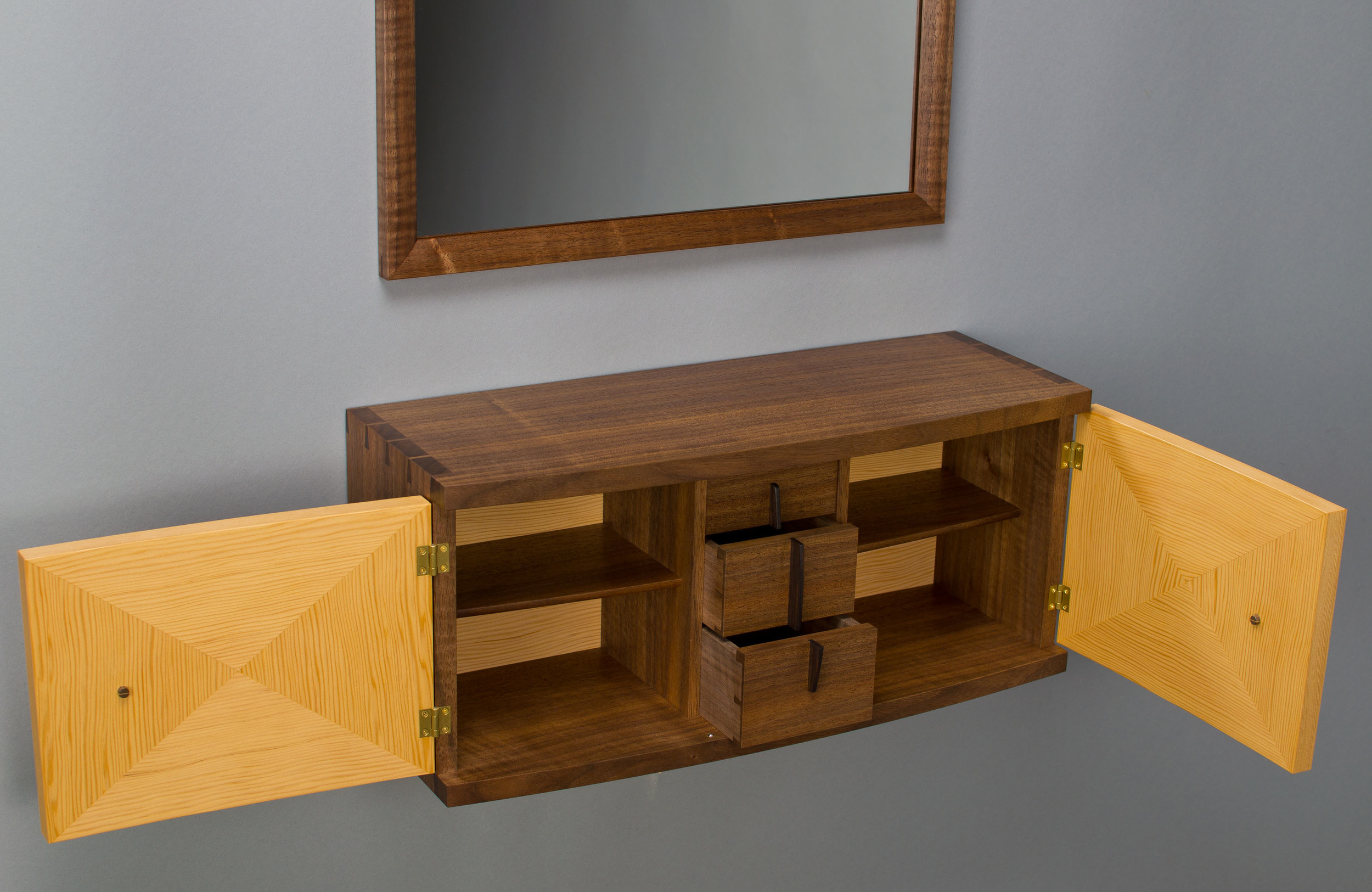
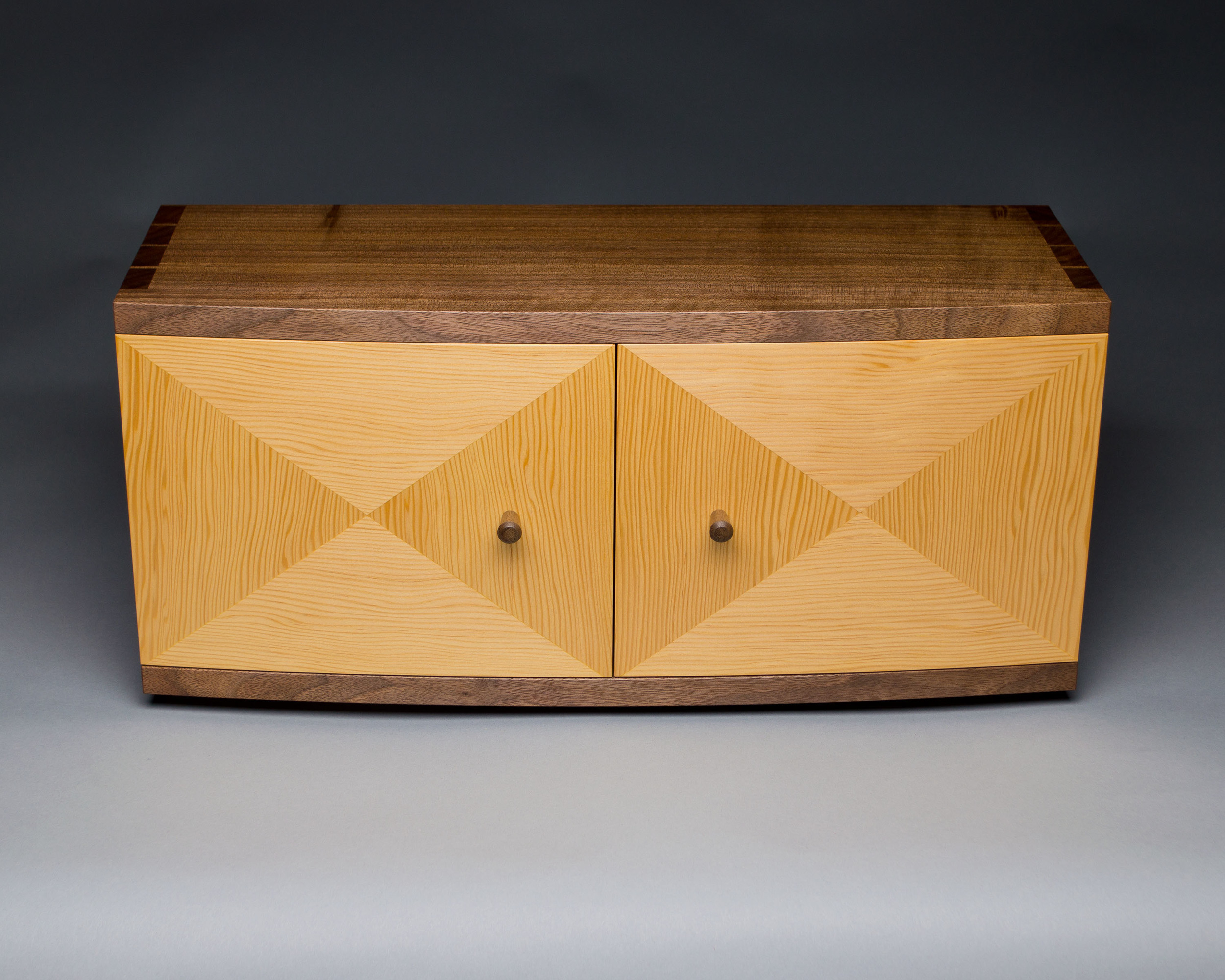
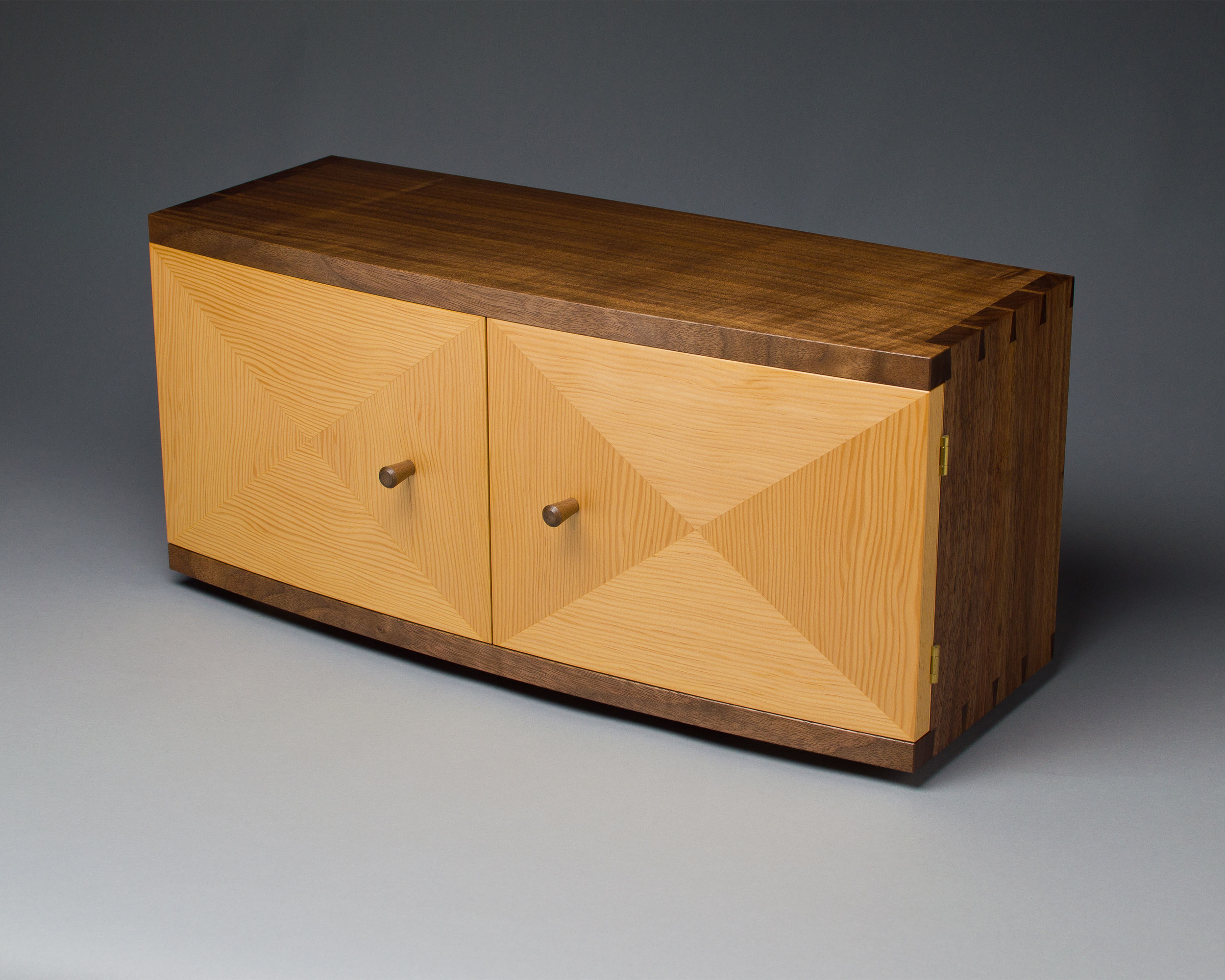
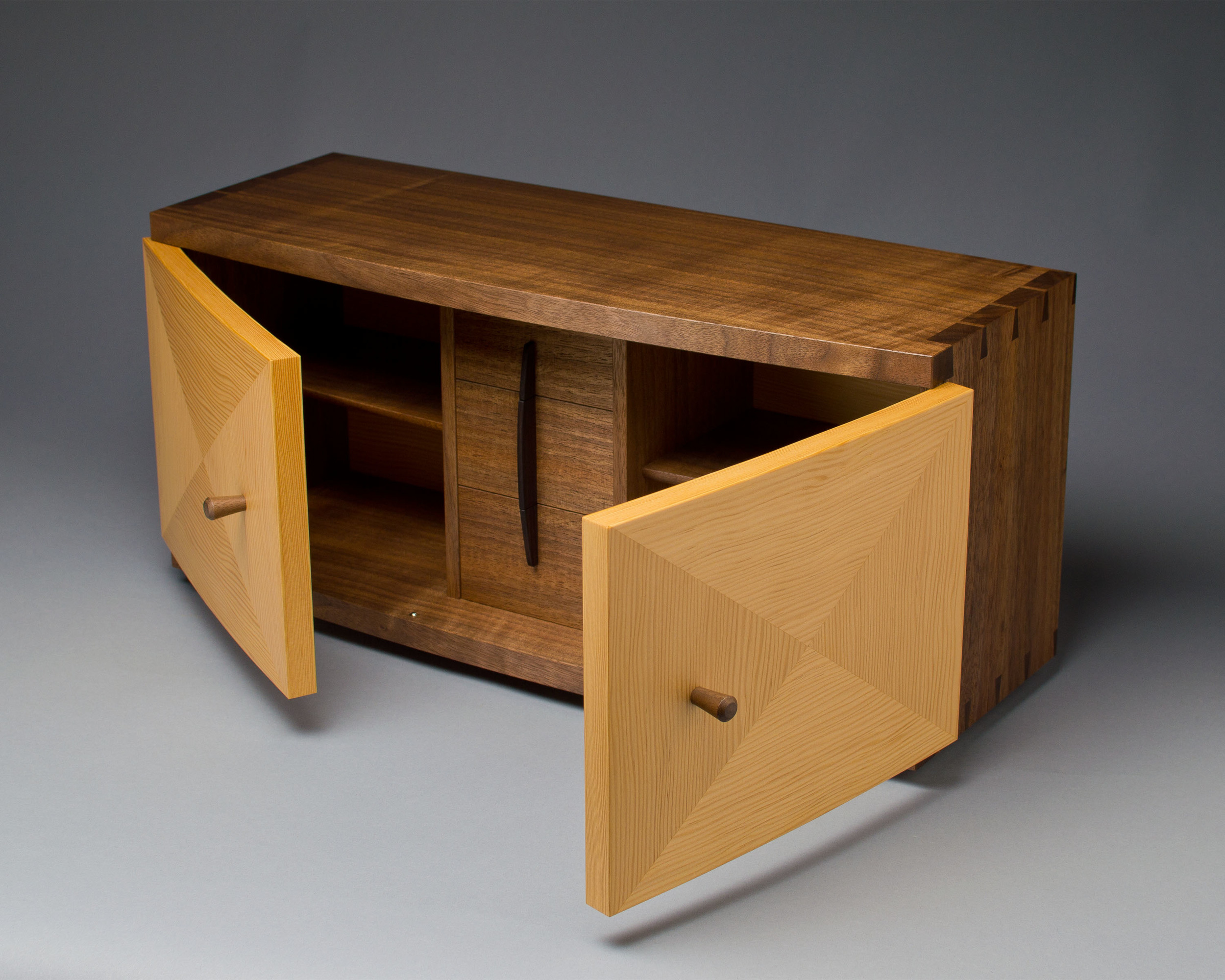
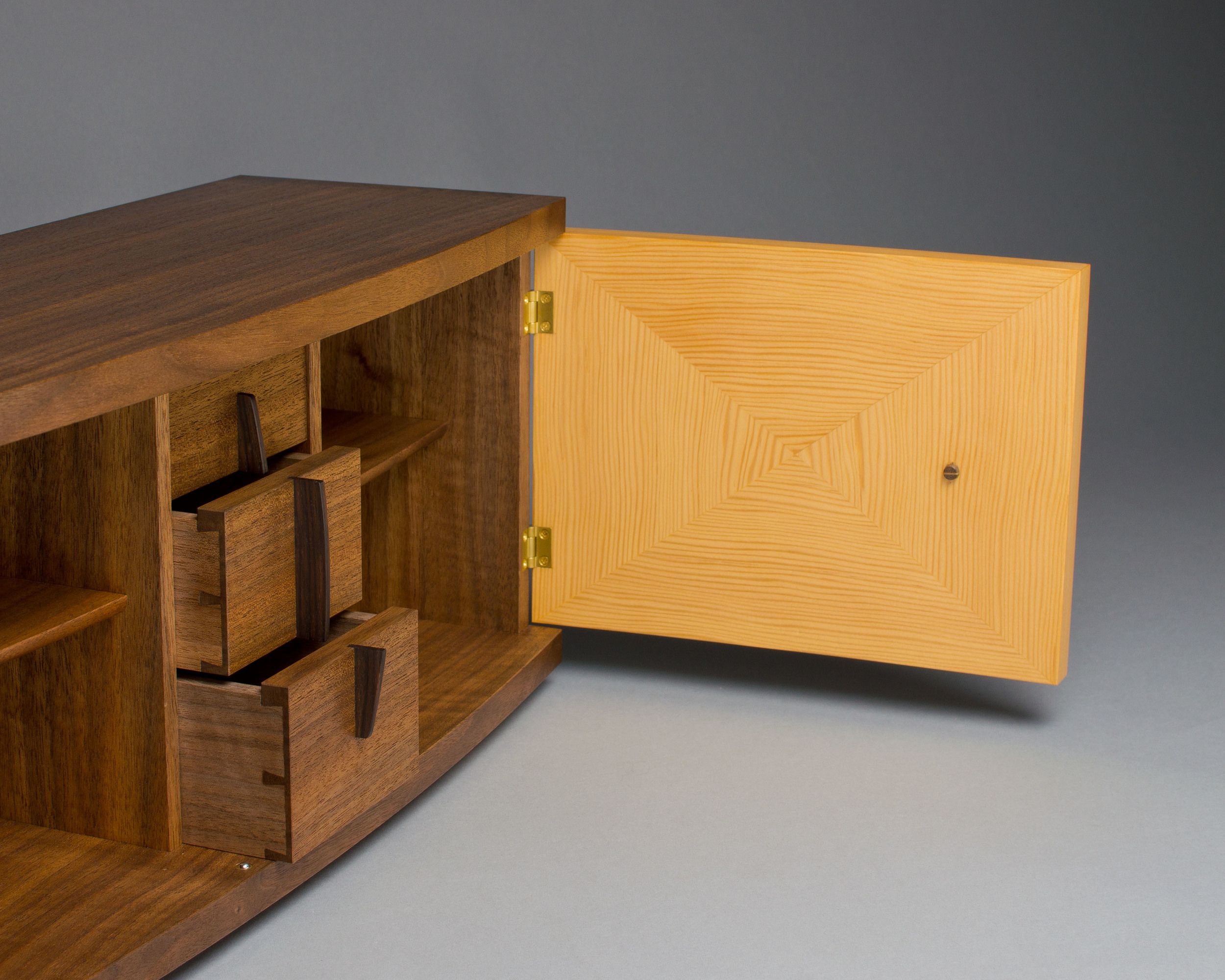